Introduction
When assessing an insurance claim for roof damage, signs might initially point toward storm-induced damage. However, a closer look may reveal an absence of correlating evidence or weather indicators. Could the cause of the shingle anomaly be from a manufacturing defect?
Anomalies on asphalt composition shingles from manufacturing flaws are rare, but they can happen. The responsibility falls on you, as the adjuster, to know the difference between normal wear, storm damage, and manufacturing defects in already installed shingles.
The asphalt composition shingle manufacturing process
Understanding the manufacturing process can help you when inspecting roof damage in the field. The process involves:
- Dry looping: Rolling out and preparing the base mat, typically fiberglass.
- Saturation: Soaking the base mat in hot liquid asphalt bitumen.
- Coating: Applying a layer of ceramic granules to protect the shingle further.
- Shaping: The shingles shape is cut from a full-size roll of material.
- Adhesion: A strip of sealant is added to the underside so shingles stick together after installation, architectural shingles are comprised of multiple layers laminated together.
- Packaging: Machines count/organize/stack/package bundles for shipping.
It’s worth noting that, despite stringent quality control measures, factors such as human error, machinery malfunctions, and inconsistencies in raw materials can introduce imperfections throughout the process. The way shingles are handled post-production, especially during storage and transportation, can also affect their quality.
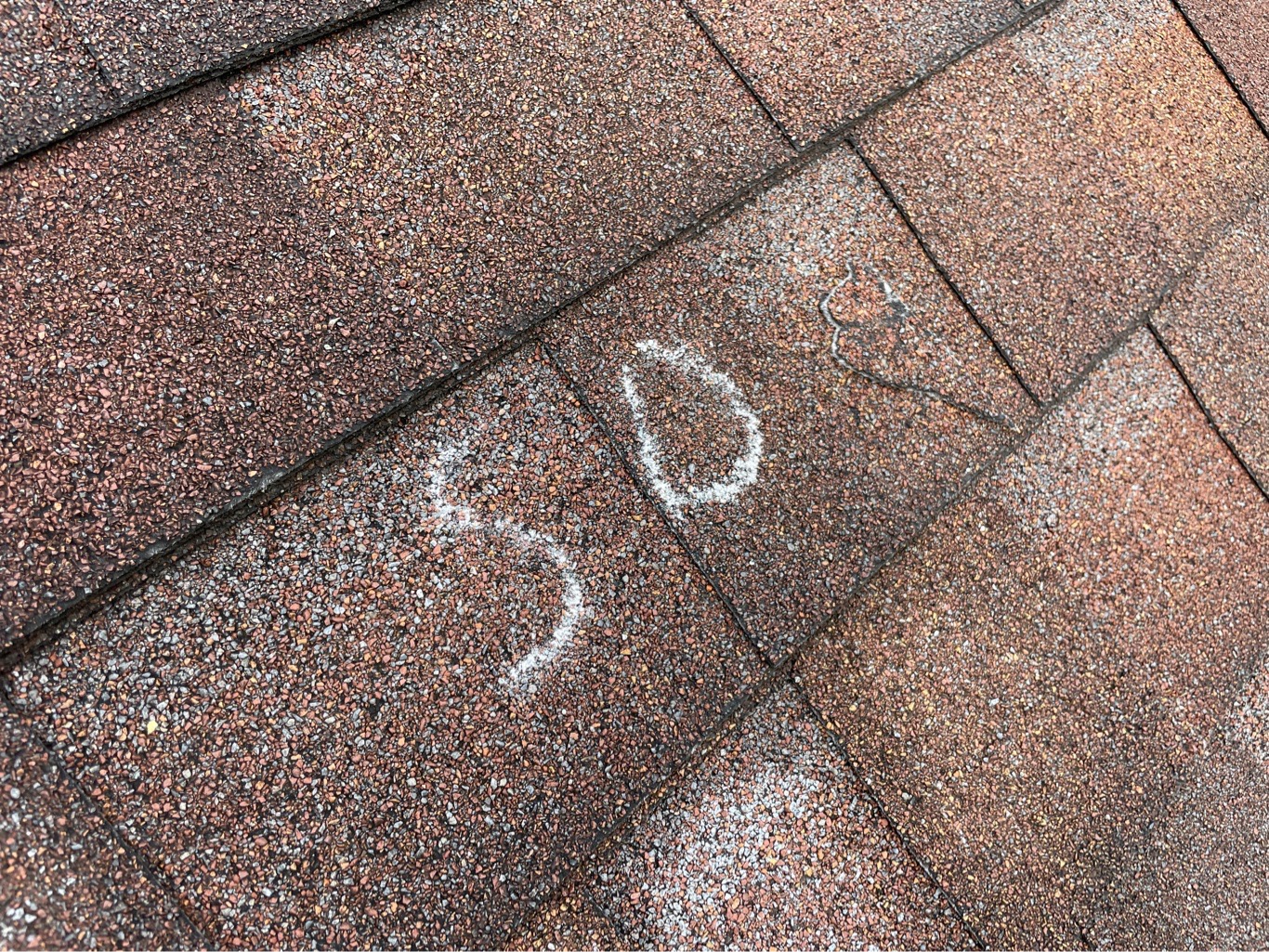
How to spot “spot defects” in shingles
At times, defects in shingles can mimic typical storm damage. Recognizing the nuanced differences can impact the way a claim is processed, safeguarding both the insurer and the policyholder from possible disagreements.
Here’s a quick guide to understanding if imperfections in shingles are the result of a manufacturing flaw or storm-related damage.
Granule Bonding
A granule bonding defect differs from normal granule loss (age and deterioration) in that it is the result of defective raw materials and/or problems in the manufacturing process. A few things that can lead to a granule bonding defect are moisture or foreign objects being introduced into the manufacturing process, the temperature of the asphalt bitumen during production, or equipment malfunctions that aren’t caught during quality control.
- Manufacturing defect indicator: Condition is widespread, level of consistency across directional slopes that isn’t the result of normal weathering (south and west facing slopes experiencing higher rates of granule loss), especially on a young roofing system.
- Storm damage: N/A
- Normal wear: South and west-facing slopes experiencing higher rates of granule loss due to weathering, north-facing slopes experiencing the least amount of granule loss
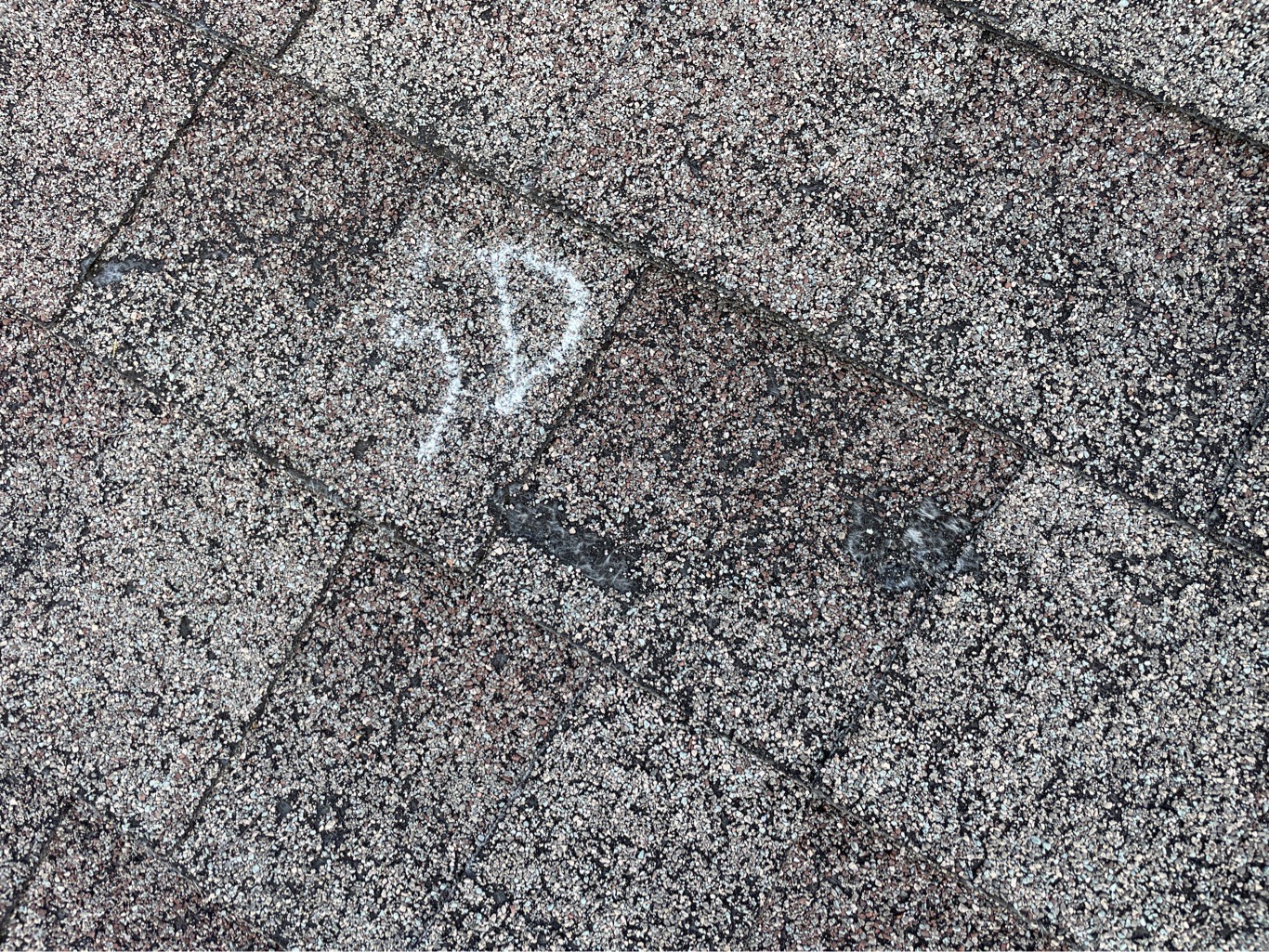
Material Handling
How shingles are handled can have a substantial impact on the overall appearance and condition of the final product. Handling materials improperly can leave behind unsightly anomalies such as scuffs, tears, or creases. Additionally, these anomalies can sometimes be misconstrued for potential storm-related damage. Material handling defects can arise from forklifts, ladder elevators, or handling by an installer.
- Manufacturing defect indicator: Anomalies are localized, scuffs/tears/creases that are not consistent with storm-related damage and can usually be attributed to poor handling, either during shipping, installation or during repairs.
- Storm damage: Marring/punctures/blunt force trauma that could be covered by an insurance policy are almost always accompanied by correlating evidence such as wood fibers embedded in the granules from a tree strike.
- Normal wear: N/A
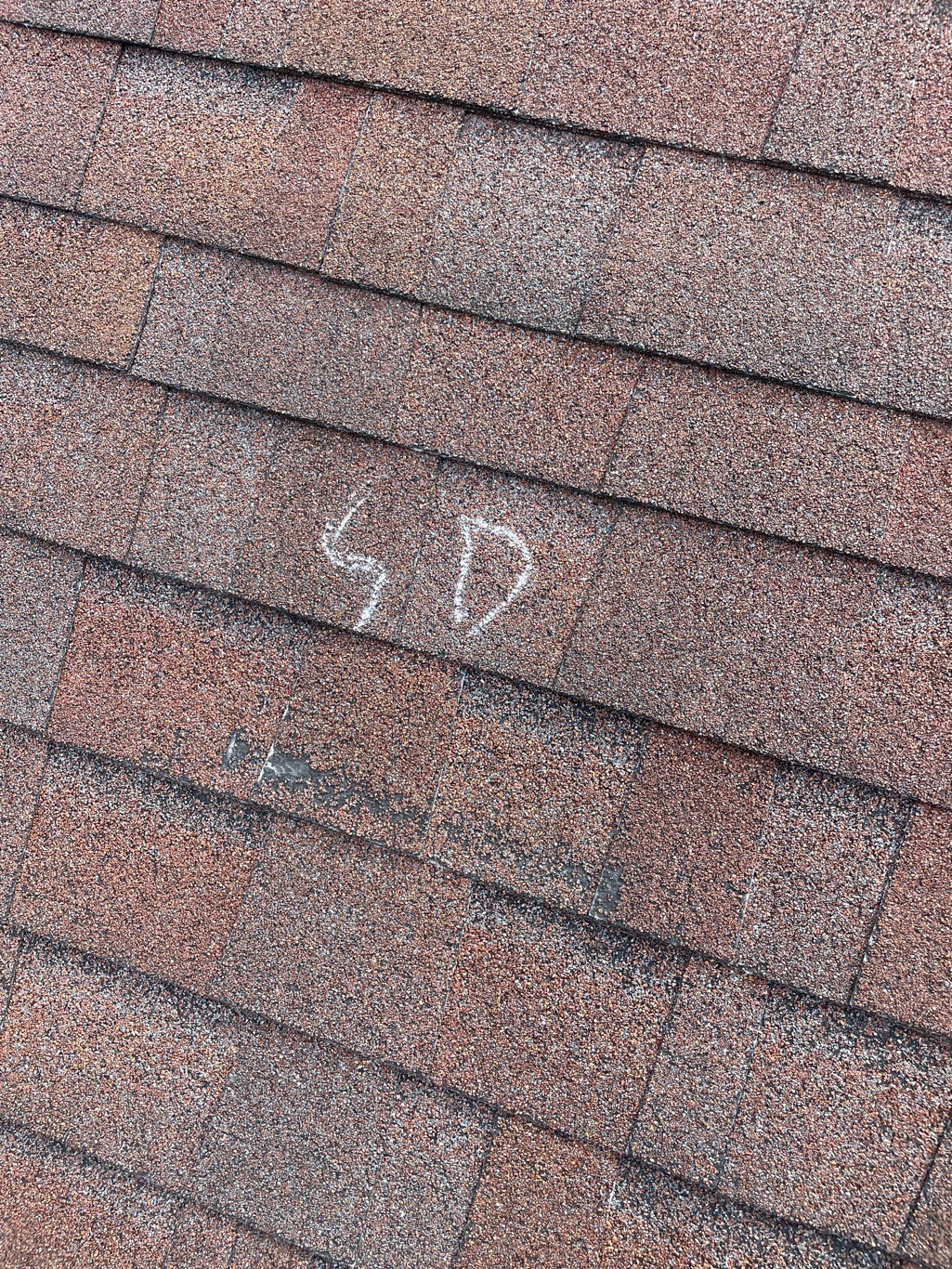
Thermal cracking
You might not be able to see thermal cracking from a ground inspection. Utilizing ladder assist for roof inspections can help adjusters better understand the overall health of a roofing system in addition to the presence of storm-related damage. Thermal cracking can be an indicator of a manufacturing error but can also be the result of poor installation, specifically around the topic of ventilation.
- Manufacturing defect indicator: Condition is widespread, especially across south/west facing slopes which receive the most direct sunshine and weathering.
- Storm damage: N/A
- Normal wear: Thermal cracking is not widespread, limited to areas of poor ventilation
Color variations
A defect that many overlook is the discrepancy of color. While roofs aren’t usually an act of artistic expression, many homeowners choose their colors in accordance with other materials to achieve curb appeal. Shingles that aren’t uniform in color can leave an unsightly eye sore for homeowners and potential buyers.
- Manufacturing defect indicator: Shingles are uniform in size/shape/age/manufacturer but appear different in color from the ground.
- Storm damage: N/A
- Normal wear: Shingles will fade in color over time, or experience a build-up of oxidation, but fading and/or oxidation should happen at similar rates according to the direction of the slope.
Tips for claims adjusters
When assessing roofs, your knowledge and expertise are instrumental. It’s also crucial to bear in mind the expected lifespan of roofing shingles. Often, claims may revolve around the question, “How long do roofing shingles last?” Manufacturing defects and environmental factors can affect a roof’s average life span.
While understanding potential manufacturing flaws is essential, tools like moisture meters and infrared cameras can provide further clarity. Collaborating with roofing inspection professionals is another tool you can lean on. Ladder assist services offer a secure and efficient method for inspecting roofs. When you need an extra layer of professional insight, Knight’s Solutions is at your service. Our extensive inspection services are available for booking directly through our online portal.
Knight’s Solutions technicians conduct inspections and provide emergency services, guided by the acting adjuster. Our HAAG-certified professionals utilize technology to provide thorough documentation, offering advisory support to insurance adjusters. Operating independently of insurance companies, our non-binding assessments provide an impartial perspective, assisting in informed decisions on potential damage. Not licensed claims adjusters, we acknowledge the final decision rests with the insurance company and designated adjuster regarding the validity of our documentation and claim settlements.
Recent Comments