Storms and hail damage are common culprits of roof damage. But some types of damage, like roof blistering, aren’t storm-related. This guide can help claims adjusters identify the difference between hail damage and shingle blistering.
What is Roof Blistering?
Shingle blistering occurs when imperfections (i.e., blisters) form on the surface of asphalt composition shingles. While it can be mistaken for hail damage, blisters aren’t caused by storms. Blistering is the result of defective asphalt bitumen used in the production of asphalt composition shingles. Bitumen is a byproduct of the crude oil refinement process. When too many hydrocarbons are left behind in asphalt bitumen, it causes a micro explosion once a shingle is installed on a roof and reaches a certain temperature. The micro explosion kicks granules off the top of the shingle, exposing the binder material and/or the fiberglass reinforcement mat.
How to Spot Shingle Blistering
Blistering will almost always occur early on in the lifespan of an asphalt composition shingle and has its telltale signs. However, identifying shingle blistering isn’t always straightforward, especially once the weathering process has continued for many years after the blistering has actually occurred. Here’s what to look for:
-
- Rigid sidewalls of an exposed area of bitumen or fiberglass
-
- Size variations, from 1 to several millimeters
-
- Not all blisters pop, some just bubble
-
- Groupings or widespread, blistering is usually a prominent condition
-
- No collateral evidence to support hail damage assessment
Photo Examples
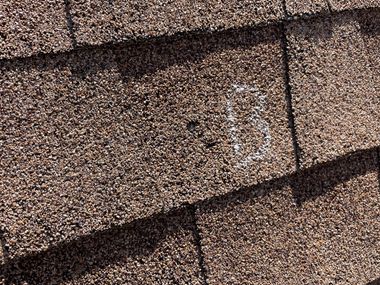
[Blistering on an architectural shingle]
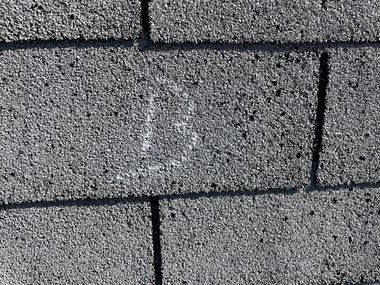
[Blistering on a three-tab shingle]
Causes of Blistered Shingles
Roof blistering is a condition associated with asphalt composition shingles and typically occurs within the first year. The two most prominent factors that can lead to blistering are leftover hydrocarbons in the asphalt bitumen from the crude oil refinement process and poor/insufficient ventilation of a roofing system.
Hydrocarbons
Asphalt bitumen used in shingle manufacturing is a byproduct of the crude oil refinement process. Although there are strict measures put in place to control the quality of asphalt bitumen, sometimes the refinement process is not perfect and too many hydrocarbons can be left behind during the refinement process. When this is the case, the hydrocarbons cause a microexplosion once installed on a roof and they reach the limits of heat exposure. The microexplosion kicks granules off the top of the shingle leaving the asphalt bitumen/fiberglass reinforcement mat exposed for weathering to take over. The ceramic granules used in shingle production, which are specifically designed to protect the asphalt from weathering too quickly, are no longer protecting the other materials when blistering occurs.
Poor Ventilation
It’s easy to blame blistering on a manufacturing defect, but poor ventilation is the most common factor that exacerbates blistering. When a roofing system is not properly ventilated, from the eaves to the ridge, with the proper amount/capacity of ventilating points, the excessive heat trapped causes the temperature of shingles to exceed their intended application. When materials are pushed past their intended limits of use, accelerated degradation takes place.
Hail Damage vs. Blistering: What’s the Difference?
Roof blisters and hail damage can sometimes look very similar in appearance. Old blistering that has been weathered for many years can easily resemble a hail strike. To accurately assess evidence observed on any inspection, knowing the difference between hail damage and shingle blistering is vital.
Hail Damage
Hailstones can have a direct and forceful impact that causes significant roof damage. Here’s what to look for:
-
- Fracturing in the asphalt bitumen/fiberglass reinforcement mat of roof shingles
-
- Concave impressions, embedded/crushed ceramic granules in shingles
-
- Excessive granule loss that is consistent & correlates with collateral damage observed
-
- Elements of randomness across slopes affected by hail
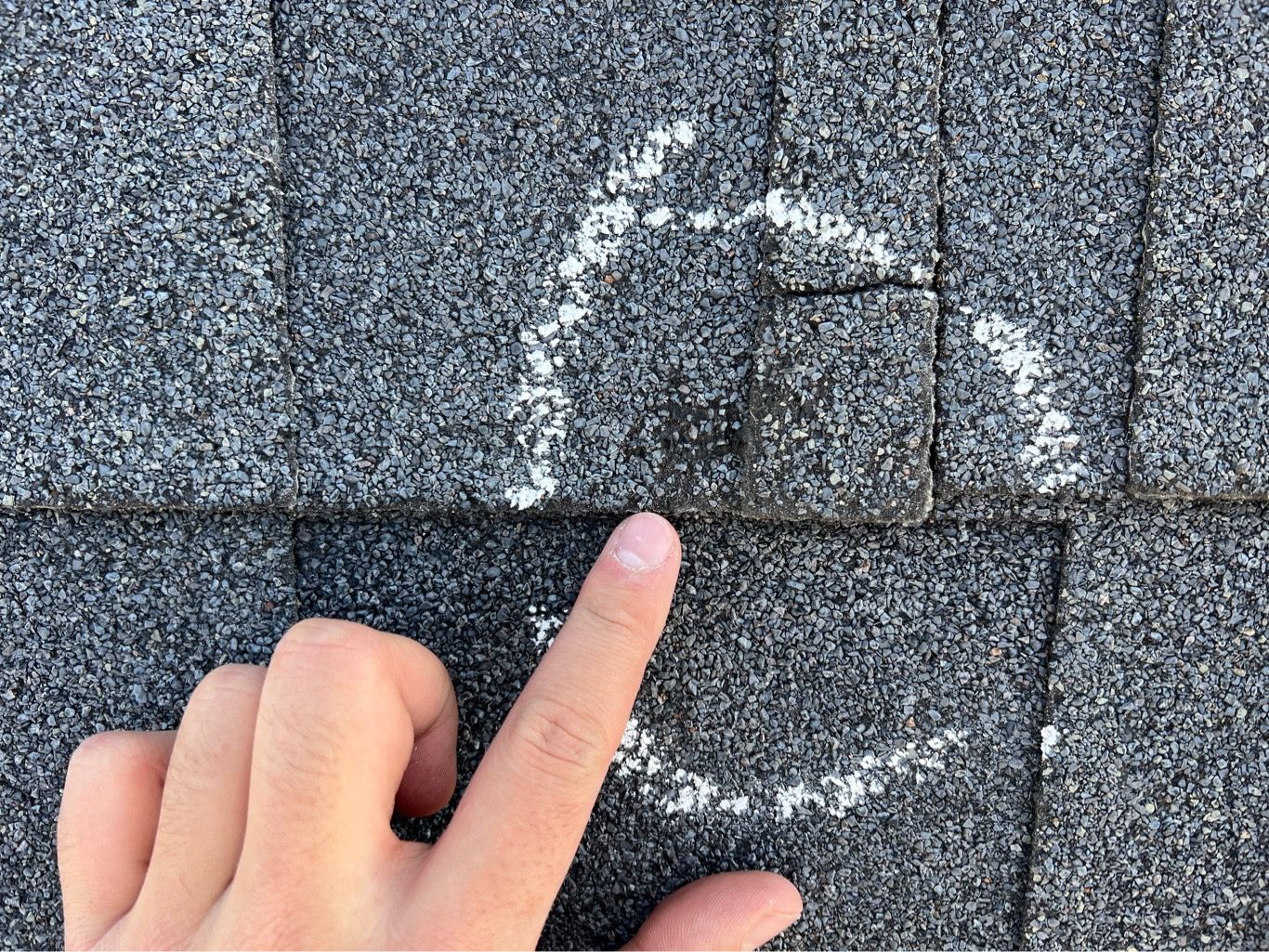
[Hail damage on an architectural shingle]

[Hail damage on an architectural shingle]
Asphalt Shingle Blisters
Blistering in shingles is typically unrelated to storm damage. But popped blisters can mimic the appearance of hail damage. Here’s what to look for:
-
- Rigid sidewalls of a blister if it’s still young and unweathered
-
- Prominent condition observed across slopes regardless of pitch
-
- No concave impression as seen with the impact of a hailstone
-
- No fracturing/bruising of asphalt bitumen
-
- Inadequate ventilation or a combination of ventilation types that don’t work well together
Other Clues to Look For
Besides the direct signs on shingles, other factors can help you determine the source of roof damage. Look for these additional clues:
-
- Collateral damage to soft metals suggest hail damage.
-
- Spatter marks on heavily oxidized surfaces indicate recent hail activity
-
- The size of spatter marks/collateral damage gives a great reference for potential max hail size
-
- Material damage thresholds – pea size spatter produced from ¼” hail will not produce damage on asphalt composition shingles
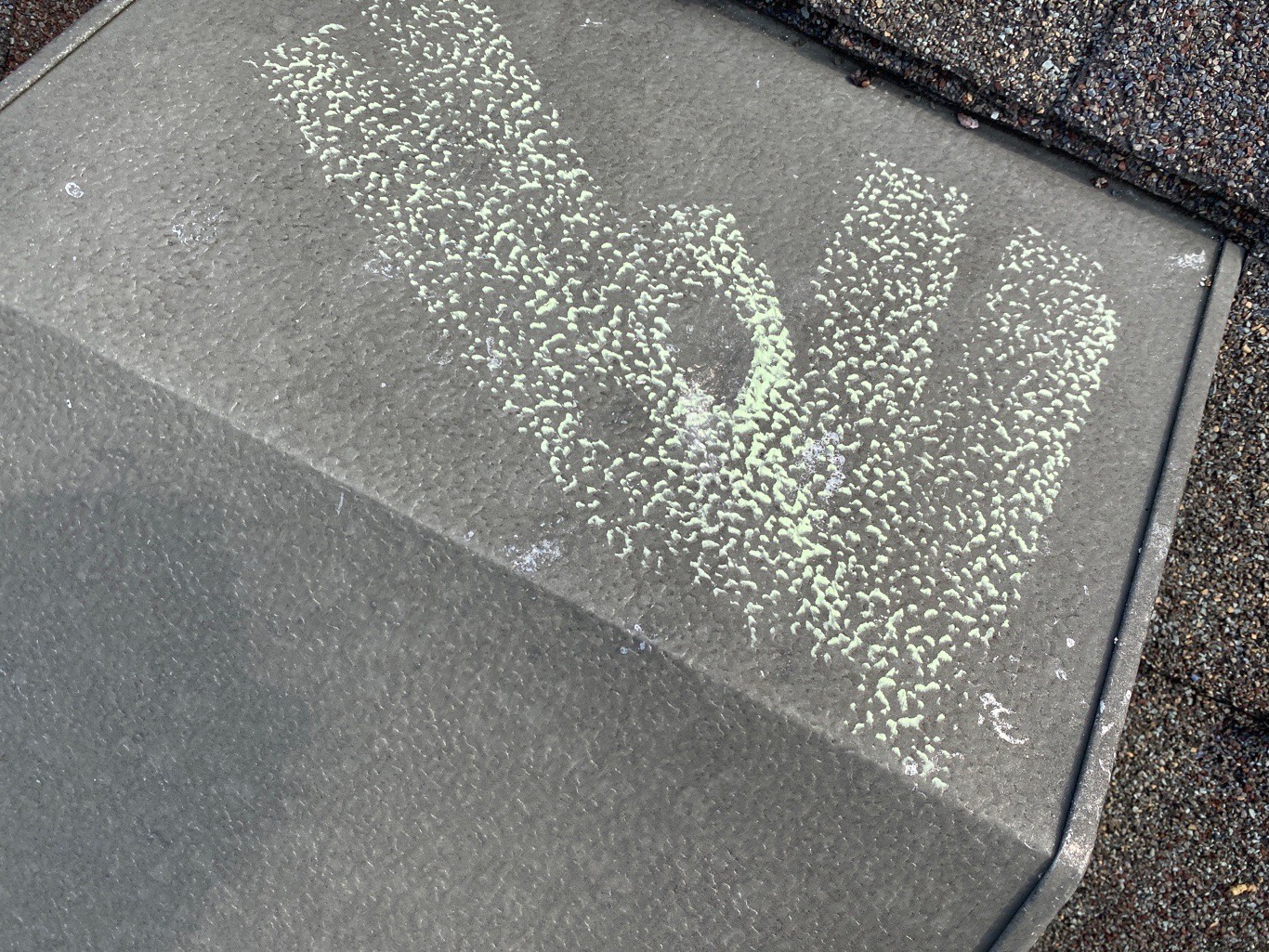
[Hail damage to aluminum box vent]
Dealing with a Damaged Roof During Inspection
When conducting inspections, exercise caution to maintain the current roof condition. Walking on shingles can cause additional damage if proper precautions aren’t taken. That’s why we utilize our Cougar Paws during an inspection, the thick foam pads provide traction and mitigate damage from foot traffic. Our goal is to leave the roof in the same condition we found it in, barring a tarp installation, ITEL Sample retrieval, or the performance of a Brittleness Test, which only occurs at the discretion of the acting adjuster.
When inspecting a property/roofing system for possible damages, the details can make all the difference. At Knight’s Solutions, our technicians provide detailed photo reports to easily determine whether or not damages are storm-related. To streamline the process, we’ve rolled out a new portal for scheduling, updates, and report access. Make your caseload more manageable by scheduling an inspection with Knight’s Solutions today.
Knight’s Solutions technicians conduct inspections and provide emergency services, guided by the acting adjuster. Our HAAG-certified professionals utilize technology to provide thorough documentation, offering advisory support to insurance adjusters. Operating independently of insurance companies, our non-binding assessments provide an impartial perspective, assisting in informed decisions on potential damage. Not licensed claims adjusters, we acknowledge the final decision rests with the insurance company and designated adjuster regarding the validity of our documentation and claim settlements.
Recent Comments